Automatische Qualitätskontrolle bezeichnet den Einsatz technologischer Systeme zur kontinuierlichen Überprüfung und Sicherstellung der Produktqualität ohne manuelles Eingreifen.
Ziele der automatischen Qualitätskontrolle
Automatische Qualitätskontrolle ist ein essenzieller Bestandteil moderner industrieller Fertigungsprozesse. Sie gewährleistet gleichbleibend hohe Produktstandards, minimiert Fehler und optimiert Produktionsabläufe. Ihre zentralen Ziele lassen sich in vier Hauptbereiche unterteilen: Fehlererkennung und -korrektur, Prozessoptimierung, Einhaltung von Qualitätsstandards und Kostensenkung.
1. Fehlererkennung und -korrektur
Der wichtigste Zweck der automatisierten Qualitätskontrolle ist die frühzeitige Identifikation von Fehlern. Durch den Einsatz moderner Sensortechnologien, hochauflösender Bildverarbeitungssysteme und künstlicher Intelligenz können Abweichungen in Echtzeit erkannt und analysiert werden. Dadurch lassen sich Mängel sofort korrigieren:
- Der Ausschuss wird reduziert.
- Kostspielige Nachbearbeitungen werden vermieden.
- Produktionsprozesse laufen stabiler und effizienter.
Besonders in Hochpräzisionsbranchen wie der Elektronikfertigung oder Medizintechnik ist eine fehlerfreie Produktion essenziell, um höchste Qualitätsanforderungen zu erfüllen.
2. Prozessoptimierung und Effizienzsteigerung
Die automatische Qualitätskontrolle ermöglicht eine durchgängige Dokumentation der Prüfprozesse. Dies führt zu einer systematischen Analyse von Fehlerquellen und einer kontinuierlichen Verbesserung der Produktionsabläufe. Vorteile sind:
- Lückenlose Rückverfolgbarkeit von Qualitätsmängeln.
- Identifikation von Engpässen und Schwachstellen.
- Optimierung von Maschinenparametern für höhere Effizienz.
Ein entscheidender Vorteil ist die Steigerung der Gesamtanlageneffektivität (OEE). Durch die Reduzierung von Stillstandszeiten, die Verbesserung der Anlagennutzung und eine exakte Steuerung der Produktionsprozesse lassen sich Ausfallzeiten minimieren und die Produktivität maximieren.
3. Kostensenkung und Ressourceneffizienz
Ein weiterer Vorteil der automatischen Qualitätskontrolle liegt in der Optimierung der Betriebskosten. Durch den Einsatz intelligenter Prüfsysteme können folgende Optimierungen erzielt werden:
- Reduzierung manueller Prüfungen, wodurch Personalkosten gesenkt werden.
- Minimierung von Ausschuss und Materialverschwendung.
- Verkürzte Produktionszeiten, was zu einer effizienteren Nutzung von Maschinen führt.
Hochwertige Produkte führen zu weniger Reklamationen, steigern das Vertrauen in die Marke und ermöglichen Wettbewerbsvorteile.
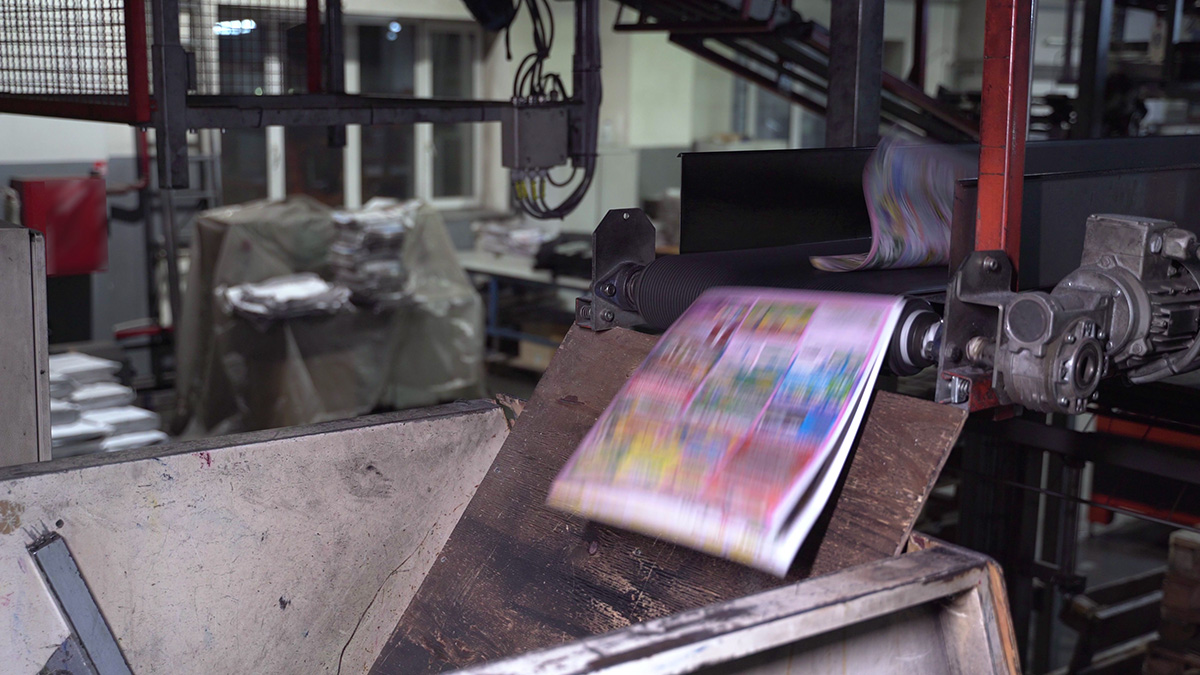
Technologien der automatischen Qualitätskontrolle
Automatische Qualitätskontrolle basiert auf einer Vielzahl fortschrittlicher Technologien, die eine präzise und zuverlässige Prüfung von Produkten in industriellen Prozessen ermöglichen. Die Auswahl der geeigneten Technik hängt von den spezifischen Anforderungen der Produktion, den zu überprüfenden Qualitätsmerkmalen und den Umgebungsbedingungen ab.
Bildverarbeitungssysteme
Optische Inspektionssysteme spielen eine zentrale Rolle in der automatischen Qualitätskontrolle. Mithilfe hochauflösender Kameras und intelligenter Algorithmen werden Produkte in Echtzeit analysiert. Diese Systeme erkennen Oberflächenfehler, Maßabweichungen und Unregelmäßigkeiten, die mit dem bloßen Auge nur schwer erfassbar wären. Durch die Kombination von 2D- und 3D-Bildverarbeitung können auch komplexe Geometrien zuverlässig geprüft werden.
Sensorik und Messtechnik
Moderne Sensortechnologien ermöglichen eine berührungslose und hochpräzise Qualitätsüberwachung. Dazu gehören:
- Laser- und Ultraschallsensoren zur Maß- und Formprüfung.
- Infrarotsensoren für die Materialanalyse.
- Druck- und Temperatursensoren zur Kontrolle kritischer Produktionsparameter.
Diese Sensoren liefern kontinuierliche Daten zur Prozessüberwachung und erlauben eine sofortige Anpassung der Fertigungsparameter.
Künstliche Intelligenz und maschinelles Lernen
Die Integration von Künstlicher Intelligenz (KI) hebt die automatische Qualitätskontrolle auf ein neues Niveau. Durch maschinelles Lernen können Prüfsysteme aus vergangenen Daten lernen, Fehlerbilder präzise klassifizieren und Anomalien frühzeitig erkennen. KI-gestützte Inspektionssysteme ermöglichen eine kontinuierliche Optimierung der Prüfprozesse, wodurch die Fehlererkennungsrate verbessert und Ausschuss reduziert wird.
Robotergestützte Inspektionssysteme
In hochautomatisierten Produktionsumgebungen kommen Roboter zum Einsatz, die Prüfaufgaben flexibel übernehmen. Diese Systeme können beispielsweise Bauteile aus verschiedenen Winkeln scannen, taktile Messungen durchführen oder fehlerhafte Produkte direkt aussortieren. Besonders in der Elektronik- und Automobilindustrie tragen solche Inspektionsroboter zu einer gleichbleibend hohen Qualität bei.
Datenanalyse und Predictive Quality
Die kontinuierliche Erfassung und Analyse von Qualitätsdaten ermöglicht vorausschauende Qualitätskontrolle (Predictive Quality). Durch die Verknüpfung von Sensordaten, Produktionsparametern und KI-gestützten Analysetools lassen sich Muster erkennen, die auf potenzielle Fehlerquellen hinweisen. So können Unternehmen Probleme bereits beheben, bevor sie zu Ausschuss oder Produktionsausfällen führen.
Ablauf der automatischen Qualitätskontrolle
Die automatische Qualitätskontrolle folgt einem strukturierten Ablauf, der sicherstellt, dass Produkte in industriellen Prozessen präzise und effizient geprüft werden. Durch den Einsatz moderner Sensorik, Bildverarbeitung und Künstlicher Intelligenz wird eine durchgängige Überwachung ermöglicht, die Fehler frühzeitig erkennt und Produktionsprozesse optimiert.
1. Datenerfassung und Sensorik
Der erste Schritt besteht in der Erfassung von Qualitätsmerkmalen. Hierbei kommen hochpräzise Sensoren, Kameras und Messsysteme zum Einsatz, die Parameter wie Maße, Oberflächenbeschaffenheit, Materialdichte oder Farbabweichungen registrieren. Je nach Anwendungsbereich werden optische, akustische oder taktile Messverfahren genutzt, um fehlerhafte Bauteile oder Abweichungen vom Sollwert zu identifizieren.
2. Echtzeit-Analyse und Fehlererkennung
Die erfassten Daten werden direkt in die Prüfsysteme eingespeist, wo sie durch Algorithmen analysiert werden. Moderne KI-gestützte Inspektionssysteme erkennen selbst kleinste Abweichungen und klassifizieren Fehler anhand von Vergleichsdaten aus vorherigen Prüfungen. Dies ermöglicht eine schnelle und präzise Identifikation von Qualitätsmängeln.
3. Automatische Entscheidung und Ausschleusung fehlerhafter Teile
Sobald ein fehlerhaftes Produkt erkannt wird, trifft das System eine Entscheidung über die Weiterverarbeitung. In vollautomatisierten Produktionslinien werden defekte Teile sofort aussortiert oder zur Nachbearbeitung gekennzeichnet. Robotergestützte Systeme können zusätzliche Eingriffe vornehmen, um fehlerhafte Komponenten zu ersetzen oder korrigierende Maßnahmen einzuleiten.
4. Prozessoptimierung und Rückmeldung an die Produktion
Ein entscheidender Vorteil der automatischen Qualitätskontrolle ist die dynamische Anpassung der Produktionsparameter. Durch die kontinuierliche Analyse der Qualitätsdaten kann das System Optimierungspotenziale erkennen und in Echtzeit Anpassungen vornehmen, um Fehlerquellen zu minimieren. So lassen sich Ausschussquoten senken und Produktionsprozesse langfristig verbessern.
5. Dokumentation und Rückverfolgbarkeit
Alle Prüfergebnisse werden in einer zentralen Datenbank gespeichert, um eine lückenlose Rückverfolgbarkeit zu gewährleisten. Dies ist insbesondere in regulierten Industrien wie der Medizintechnik, Pharma- oder Automobilbranche essenziell, um Qualitätsstandards und gesetzliche Vorgaben einzuhalten.
Fazit
Der Ablauf der automatischen Qualitätskontrolle folgt einem klaren, strukturierten Prozess, der auf Datenerfassung, Fehlererkennung, Ausschleusung, Prozessoptimierung und lückenloser Dokumentation basiert. Durch die Kombination fortschrittlicher Technologien wie KI, Bildverarbeitung und Predictive Quality können Unternehmen eine gleichbleibende Produktqualität sicherstellen und ihre Produktionsabläufe nachhaltig optimieren.
FAQ – Automatische Qualitätskontrolle
Wie unterscheiden sich Inline- und Offline-Qualitätskontrollen?
Die Inline-Qualitätskontrolle erfolgt direkt in der Produktionslinie, während das Produkt gefertigt wird. Sensoren, Kameras oder KI-gestützte Systeme überprüfen kontinuierlich die Qualität und erkennen Fehler in Echtzeit. Dadurch können Abweichungen sofort korrigiert und Ausschuss minimiert werden.
Die Offline-Qualitätskontrolle hingegen findet außerhalb der Produktionslinie statt. Produkte oder Stichproben werden aus der Fertigung entnommen und in separaten Prüfstationen analysiert. Dieses Verfahren bietet tiefere Analysen, ist jedoch zeitaufwendiger und erlaubt keine unmittelbare Korrektur im Herstellungsprozess.
Was ist Predictive Quality und wie unterscheidet sie sich von herkömmlicher Qualitätskontrolle?
Predictive Quality nutzt fortschrittliche Datenanalyse, KI und Machine Learning, um Qualitätsabweichungen bereits im Vorfeld zu erkennen und zu verhindern. Statt Fehler erst nach der Produktion oder während der laufenden Fertigung zu identifizieren, analysiert Predictive Quality historische und Echtzeitdaten, um Muster zu erkennen und Fehlentwicklungen proaktiv zu vermeiden.
Im Vergleich dazu arbeitet die herkömmliche Qualitätskontrolle reaktiv: Fehler werden erst nach ihrer Entstehung erkannt und behoben. Predictive Quality verbessert somit die Produktionsstabilität, reduziert Ausschuss und ermöglicht eine frühzeitige Optimierung der Fertigungsprozesse.
Welche Sensorarten werden für die automatische Qualitätsprüfung eingesetzt?
Für die automatische Qualitätskontrolle kommen verschiedene Sensorarten zum Einsatz, je nach den zu prüfenden Parametern:
- Optische Sensoren: Erfassen Oberflächenfehler, Maßabweichungen und Farbunterschiede durch Kameras und Bildverarbeitungssysteme.
- Laser- und Ultraschallsensoren: Messen Dimensionen, Materialdicken und Strukturabweichungen mit hoher Präzision.
- Infrarot- und Röntgensensoren: Ermöglichen die Materialprüfung und das Erkennen von inneren Defekten oder Fremdkörpern.
- Druck- und Temperatursensoren: Überwachen physikalische Eigenschaften in der Produktion, z. B. bei empfindlichen Materialien.
- Kraft- und Drehmomentsensoren: Prüfen mechanische Belastungen und Festigkeit, insbesondere in der Automobil- und Maschinenbauindustrie.
Durch den kombinierten Einsatz dieser Sensoren kann die automatische Qualitätskontrolle hochpräzise Prüfungen durchführen und Produktionsprozesse in Echtzeit optimieren.